The Evolution and Importance of Automotive Molds in the Automotive Industry
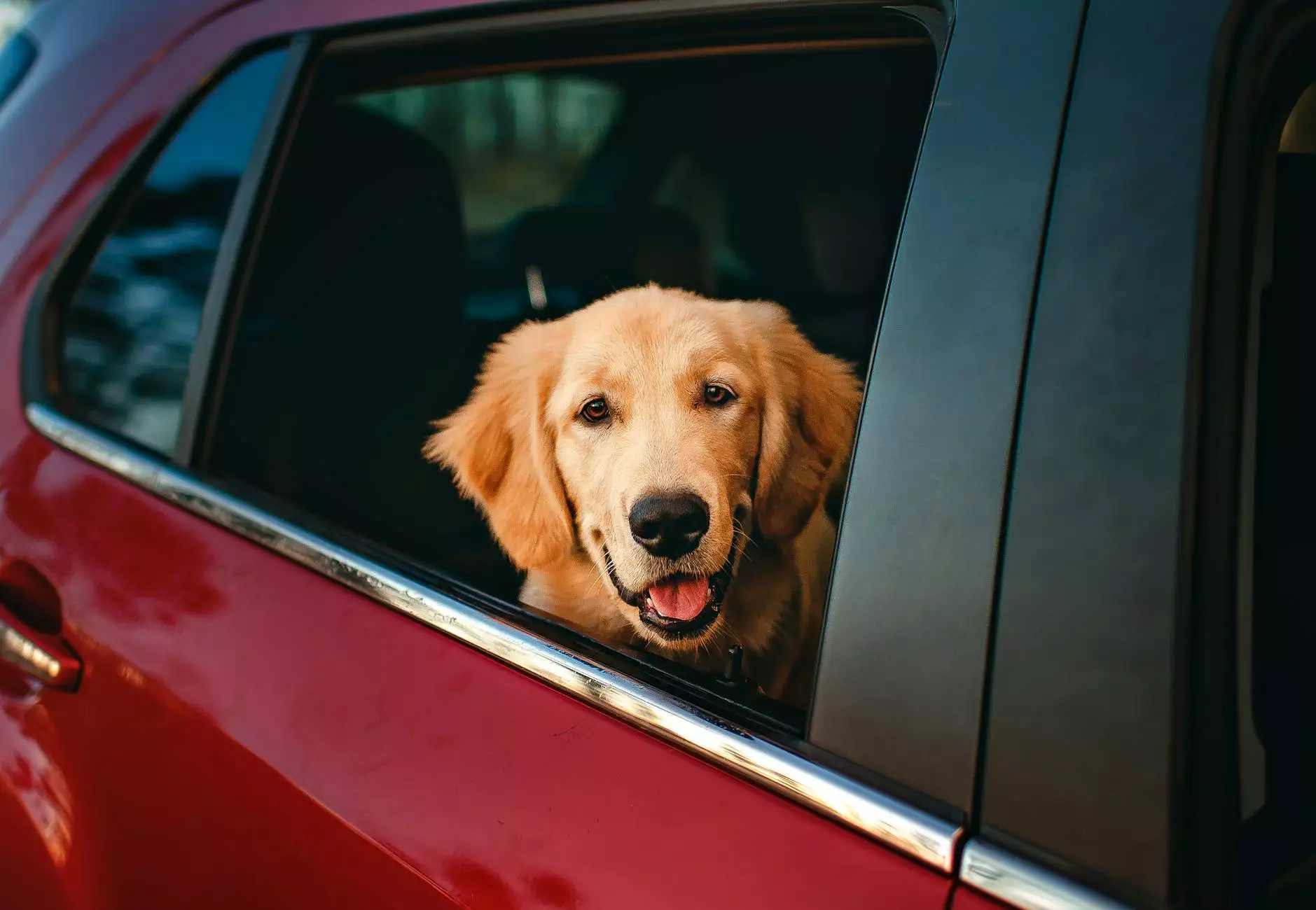
The automotive industry has always been at the forefront of innovation and efficiency. One of the key components that contribute to this progress is the use of automotive molds. These molds play a critical role in the manufacturing process, ensuring that vehicles are produced with precision, durability, and efficiency. In this article, we will explore the significance of automotive molds, their evolution, and what manufacturers need to know when working with metal fabricators like those at DeepMould.net.
Understanding Automotive Molds
Automotive molds are specialized tools used in the automotive manufacturing process to shape materials into components that meet specific design criteria. They can be made from various materials, including metals, plastics, and composites, and are designed for a range of processes such as injection molding, compression molding, and blow molding.
The Role of Automotive Molds in Production
Molds are essential for the production of numerous automotive parts, including:
- Body Panels: Outer panels such as fenders and doors.
- Interior Components: Dashboards, consoles, and trim pieces.
- Engine Parts: Covers, housings, and various supports.
- Electrical Enclosures: Components that protect wiring and electrical systems.
Each of these components needs to meet stringent performance and safety standards, making the role of automotive molds indispensable in the manufacturing process.
The Evolution of Automotive Molds
Over the decades, automotive molds have evolved significantly. The journey began with simple wooden molds that were later replaced with more durable and precise metal molds. The advent of computer-aided design (CAD) and computer-aided manufacturing (CAM) has transformed mold making, allowing for greater customization and efficiency.
Modern molds are often designed with 3D modeling software, which enables manufacturers to simulate production processes and optimize design before physical production begins. This not only saves time but also reduces material waste and increases overall productivity.
Types of Automotive Molds
Understanding the different types of automotive molds is crucial for manufacturers. Here are some common types:
Injection Molds
Injection molds are used to inject molten plastic or metal into a mold cavity. This method is prevalent for producing complex and detailed parts.
Compression Molds
Compression molds are used in processes where heated material is placed in an open, heated mold cavity. This technique is often used for producing larger parts, such as body panels.
Blow Molds
Blow molds are specifically designed for hollow plastic parts. This process involves inflating a heated plastic tube to form a hollow shape.
Thermoforming Molds
Thermoforming molds involve heating a plastic sheet and then forming it over a specific shape. This method is efficient for creating lightweight, cost-effective parts.
The Advantages of Using Automotive Molds
Utilizing high-quality automotive molds in production processes offers numerous advantages, including:
- Precision: Molds are engineered to produce components with high accuracy, ensuring that all parts fit together seamlessly.
- Durability: Quality molds can withstand the rigors of production and provide enduring performance.
- Efficiency: Automating the molding process can vastly reduce manufacturing times.
- Repeatability: Molds allow for the consistent production of parts, minimizing variations.
Choosing the Right Metal Fabricator
When it comes to creating automotive molds, selecting the right metal fabricator is crucial. Here are some key considerations:
Experience and Expertise
Look for fabricators with substantial experience in creating automotive molds. Their expertise will influence the quality of the molds produced.
Technology and Equipment
Advanced technology plays a pivotal role in the quality of automotive molds. Ensure that the fabricator uses state-of-the-art machinery and software.
Quality Assurance
Quality control is indispensable in the production process. Choose a fabricator that adheres to strict quality standards and certifications.
Customer Support
Effective communication and support are essential throughout the production process. A responsive fabricator can help troubleshoot any issues that arise.
Sustainability in Automotive Mold Manufacturing
As the automotive industry moves towards greener technologies, sustainability is becoming increasingly important. Many fabricators now focus on environmentally friendly practices, such as:
- Material Recycling: Utilizing recycled metals and plastics in mold production.
- Energy Efficiency: Implementing energy-saving measures in manufacturing processes.
- Waste Reduction: Minimizing waste during production through efficient design and planning.
Future Trends in Automotive Mold Technology
The future of automotive molds looks promising with advancements in technology. Emerging trends include:
3D Printing
3D printing technology is being increasingly utilized for creating complex mold shapes that would be challenging to manufacture through traditional methods.
Smart Manufacturing
Integration of the Internet of Things (IoT) in the manufacturing process allows for real-time monitoring and adjustments, enhancing production efficiency.
Advanced Materials
New materials that offer greater strength and lighter weights are being introduced, allowing for innovation in mold design and functionality.
Conclusion
In summary, automotive molds are a cornerstone of the automotive manufacturing process. Their evolution has been a substantial factor in the efficiency, precision, and sustainability of vehicle production. Companies like DeepMould.net play a critical role in providing high-quality mold fabrication services that meet the stringent demands of the automotive industry. As technology continues to advance, so too will the capabilities of automotive molds, paving the way for a more efficient and environmentally friendly future.
For manufacturers looking to innovate and enhance their production processes, understanding the significance of automotive molds is essential. By partnering with leading metal fabricators, businesses can realize the full potential of their automotive designs, ensuring not only the success of their products but also the sustainability of their practices in an ever-evolving industry.